اصول طراحی قالب دایکست :
وقتی صحبت از طراحی قالب دایکست پیش می آید ، آشنایی با فرایند تزریق قالب دایکست و موارد حساس در تولید قطعات آلومینیومی با این روش ریخته گری تحت فشار قطعا لازم خواهد بود . در این مقاله سعی میشود به صورت کلی موارد مهم در طراحی فالب دایکست را بررسی نماییم .
- طراحی صحیح قطعه :
قبل از طراحی قالب ابتدا میبایست قطعه را به صورت صحیح مدلسازی سه بعدی نماییم . برای این کار قبل از هر چیز با مراجعه به نقشه دو بعدی قطعه ، تلرانسها و نقاط حساس را شناسایی میکنیم . بهترست در هنگام مدلسازی اعداد را در حد وسط تلرانس لحاظ کنیم تا در صورت بروز خظاهای ماشین کاری قطعه در محدوده مورد نظر قرار گیرد . به طور مثال اگر در نقشه دوبعدی اندازه اسمی 100 و تلرانس آن صفر تا 0.1+ مشخص شده ، عددی که در مدلسازی سه بعدی در نظر گرفته میشود 100.05 باشد .
نکته دیگر اینکه در مدلسازی سه بعدی همه دیواره های قطعه میبایست زاویه خروج داشته باشد . این عدد از 0.5 درجه تا 2 درجه بسته به میزان در گیری قطعه در قالب متغییر میباشد و اگر محدودیتی به لحاظ فرم و شکل هندسی و عملکرد قطعه وجود ندارد هرچقدر این مقدار بیشتر باشد بهترست . ولی به طور کلی استفاده از زاویه 1 درجه در سطوح مناسب میباشد . با دستورات کنترل زاویه در نرم افزارها میتوان سطوح را مدام کنترل کنرد تا سطحی بدون زاویه یا undercut ( زاویه منفی ) وجود نداشته باشد . در مدلسازی بهتر است هر حجمی را که ترسیم کردیم زاویه آن را همان موقع ایجاد کنیم و اینگونه نباشد که قطعه را کامل طراحی کنیم و در انتها شروع به ایجاد زوایا نماییم . این کار باعث بروز محدودیتها و اشکالاتی در مدلسازی میشود .
نکته دیگر در مدلسازی سه بعدی قطعات قالب ، حذف گوشه های تیز در قطعه بجز خط جدایش میباشد . برای این کار نمام گوشه های تیز با دستورات fillet گرد میشود . داشتن فیلت در گوشه ها هم باعث کاهش تمرکز تنش در قطعه شده هم جداشدن قطعه را از قالب راحت تر میکند و هم باعث زیباتر شدن قطعه میشو د. توجه داشته باشید که در صورت نداشتن محدودیت گوشه ها را حداقل R1 بزنید . و اینکه اجرای فیلیت در انتهای مدلسازی باشد . در اخر اعمال شرینکیج یا ضریب انبساط حجمی ( درصد جبران انقباض مذاب پس از انجماد ) که این مقدار برای قالب دایکست عدد 0.6 درصد یا scale : 1.006 میباشد .
تجربه نشان داده است که بهترین روش جهت جلوگیری از خطای طراحی ، ایجاد نقشه دوبعدی در محیط drawing نرم افزار از فایل یه بعدی ایجاد شده مطابق نقشه دوبعدی موجود و مقایسه این دو با هم میباشد . این کار هرگونه خطای طراحی را نشان داده که با اصلاح آن از صحت فایل قطعه قبل از قالب گیری مطمن میشویم .
و درنهایت طراحی قالب با رعایت استاندارد ها و پروتکل های صحیح طراحی . در این قسمت پس از گرفتن core و cavity بهترست یکبار قطعه را در نرم افزار شبیه ساز تحلیل دمایی کنید تا بهترین مسیر راهگاهی را در قالب اعمال نمایید .
ابعاد کویته ها با توجه به فرم هندسی ابعاد قطعه مشخص میشود ولی بهتر است از لبه های قطعه تا لبه کویته حداقل 80 میلیمتر فاصله دهید تا هم فضای مناسب جهت قرارگیری اور فلو ها وجود داشته باشد هم سطح اب بند قالب به حدی باشد که اصطلاحا قالب پاشش نکند .
در مقاله بعد در مورد شیوه های طراحی قالب شامل : جنس مواد اولیه اجزا قالب ، محل و تعداد پران ها ( سیستمejector ) ، ابعاد و فرم گیت ورودی راهگاه ، محل و ابعاد اور فلو ها ، محل و ابعاد مسیر راه آب های خنک کاری ( سیستم cooling ) قالب ، ابعاد و فرم کفشک قالب ، فرم و ابعاد پل ها ، نحوه و میزان عملیات حرارتی کویته های قالب ، سیستم کشویی ها و … موارد اجرایی تجربی و علمی لازم را عنوان خواهیم کرد .
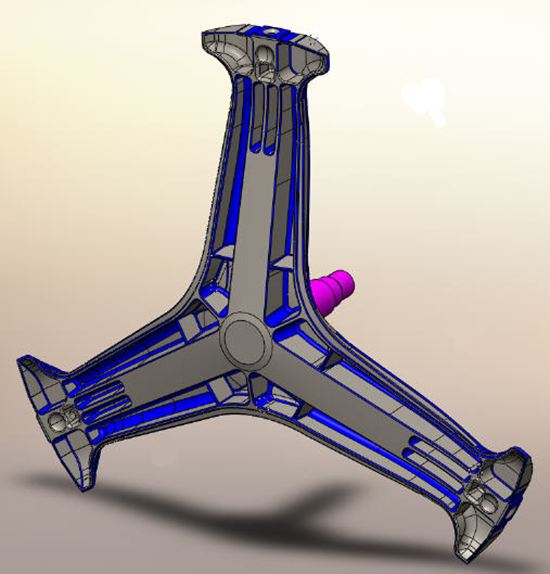
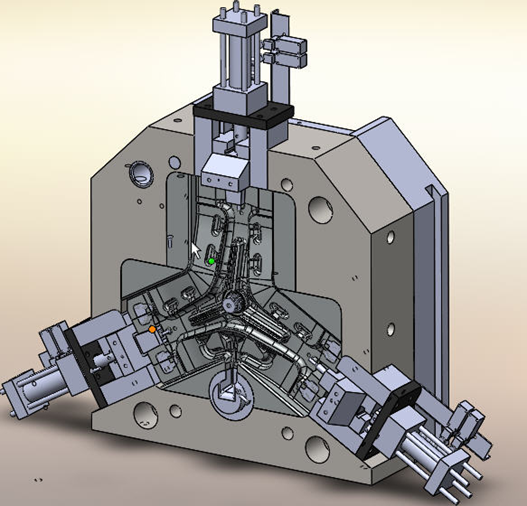